Petfood Smart Extruder Automation
Project Summary
DAD’S Products Company — a $60-million manufacturer of canned, dry, and soft-moist dog and cat food — looked to Bachelor Controls to minimize waste and reduce the load on the wastewater treatment facility.
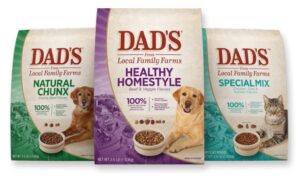
Objectives / Requirements
Minimize slurry end-of-run waste to reduce the load on the wastewater treatment facility, including:
- Handle the wet additive independently rather than in a batch slurry, so slurries can be more generic across products and the more specific flavor and preservative ingredients can be metered at the extruder
- Automate the ingredient feed system and meter ingredients into the dry feed system at the extruder pre-conditioner
- Integrate the extruder formula setup/management system so that each formula must be linked to a product that has been defined and resides in the batching SQL Server database
- Add two additional Readco/Bonnot units to the core BCI AUTOPILOT® configuration and control all three units from a single operator interface
- Monitor process performance and quality
Results / Benefits
The amount of waste material going to the water treatment facility during change-overs was reduced, producing:
- 10 percent increase in yields
- More than 40 percent increase in production throughput
- 66 percent improvement in change-over times, from 90 minutes to 30 minutesDADS – cat+family
- “Enormous improvement” in product quality — in terms of shape, color and consistency (Jeff Lang)
- Eliminated extruder set-up errors against the dry mix product to be run by synchronizing the batch systems’ Batch Campaign Management and extruder’s Formula Selection screens
- Equipment-independent master recipes, used across production lines, have increased manufacturing throughput and flexibility
- Data for each step of the petfood production cycle are electronically collected, stored and displayed.
- The real-time link between the company’s batch process and its business planning functions enables engineers to access information, release batches, and make on-line changes to recipes from workstations across the network.
Testimonials
Bachelor’s ability to provide an installation-friendly panel should not be overlooked. The panel items were grouped, packaged and routed to enhance the installation effort. There are just a lot of little details that are a standard part of a Bachelor panel.
It’s running fantastic! I love it! We’ve broken three production records in a row. We’ve seen over a 40-percent increase in throughput on average, and we’ve seen change-over times drop by over 65 percent.